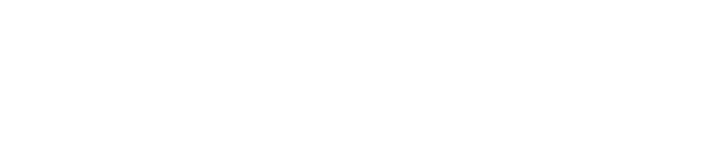
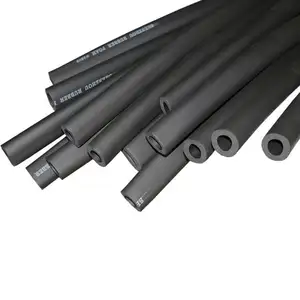
Fireproof Material Heat Shield Rubber Foam Tube Pipe Insulation For Air Conditioner Hvac Rubber Foam Pipe Insulating

In an era where energy efficiency and cost-effectiveness are paramount, understanding the role of insulation in heat conservation is crucial. This article delves into the world of rubber pipe insulation, a solution that not only conserves heat but also cuts costs. We explore the concept of heat loss, its impact, and how rubber pipe insulation can mitigate it. We'll also discuss the types of rubber pipe insulation, their benefits, and how to select the right one for your needs. Furthermore, we'll guide you through the installation process, cost analysis, maintenance, and longevity of rubber pipe insulation, and share some real-world success stories.
Heat loss is the intentional or unintentional movement of heat from one material to another, occurring through conduction, convection, and radiation. Factors that influence heat loss can change when you relocate a process or make changes to your assembly line. Adjusting the temperature of your heater or protecting it from heat loss factors can reduce the wattage usage of your system, saving considerable daily operating expenses. Calculating the heat loss of a system helps identify the correct product for a new line, taking into account the location, insulation type, and material being heated.
Rubber pipe insulation, also known as flexible elastomeric closed-cell foam pipe insulation, is made from synthetic rubber. The two main types available are nitrile butadiene rubber with PVC (NBR/PVC) and EPDM (Ethylene Propylene Diene Monomer). These insulations consist of a closed-cell structure, efficiently controlling condensation on cold piping systems. They meet the industry reference standard ASTM C 534, indicating their quality and reliability. This insulation type is ideal for commercial and industrial applications due to its lower thermal conductivity, higher continuous operating temperature, and predictable fire behavior.
Rubber pipe insulation, specifically flexible elastomeric closed-cell foam, offers several benefits. It has a lower thermal conductivity than foam plastic, making it more thermally efficient. It can withstand higher continuous operating temperatures, with NBR/PVC foam rubber at 220℉ [104℃] and EPDM foam rubber at 257℉ [125℃]. In terms of fire safety, rubber insulation is more predictable and passes ASTM E 84 or UL 723 25/50 flame spread/smoke-developed index up to 2” [50 mm] thick. Rubber insulation is also more flexible compared to foam plastic.
Insulation is a crucial element to maintain the integrity of any heating system. Heat naturally escapes most things it’s inside of, so insulation helps slow this process down. It does that by enhancing the effectiveness of heat transportation, preventing energy loss, and reducing operational costs. A well-insulated system ensures that heat energy is evenly distributed, reaching its intended destination while minimizing waste. Pipe insulation also contributes to the sustainability of heating systems by reducing carbon emissions.
Rubber pipe insulation, also known as flexible elastomeric closed-cell foam, is primarily composed of synthetic rubber. The two main types commercially available are nitrile butadiene rubber with PVC (NBR/PVC) and EPDM (Ethylene Propylene Diene Monomer). Both types consist of a closed-cell structure, controlling condensation efficiently on cold piping systems. NBR/PVC foam rubber can withstand temperatures up to 220℉ [104℃], while EPDM foam rubber can handle up to 257℉ [125℃]. The choice between these types depends on the application, considering factors like thermal conductivity, continuous service temperature, fire safety, and cost.
Selecting the right rubber pipe insulation depends on several factors. Foam rubber typically offers better thermal efficiency than foam plastic. It also has a higher continuous operating temperature, with NBR/PVC foam rubber at 220℉ [104℃] and EPDM foam rubber at 257℉ [125℃]. Fire safety is another crucial factor, with foam rubber showing more predictable behavior. When comparing NBR/PVC and EPDM, consider factors like chemical polarity, thermal conductivity, water vapor permeability, corrosiveness, UV resistance, mold resistance, PVC content, and flexibility in cold weather. The right type of rubber insulation is nonpolar, non-corrosive, UV-resistant, and stays flexible in cold weather.
To install rubber pipe insulation, first measure the total length of pipes you will insulate and determine the pipe diameter and the R-value of the insulation needed. Cut the tube to the measured length and then cut through the wall thickness on one side along the entire length of the tube. Open the tube and place it so it wraps around the pipe. If the tube has pre-applied adhesive strips, peel back the paper to expose the adhesive and press down on it. If there is no adhesive strip, secure the tube in place on the pipe with duct tape or zip ties.
When it comes to cost, foam plastic typically costs less than rubber. However, the project application, performance characteristics, and owner project requirements may be more important than the initial cost. Rubber pipe insulation, despite being more expensive initially, offers lower thermal conductivity, higher continuous operating temperature, and more predictable fire behavior. These factors can lead to long-term savings in energy costs and maintenance, making rubber a cost-effective choice for commercial and industrial applications.
HVAC refrigerant line insulation, specifically rubber-based, is designed to last the life of the mechanical system it insulates, provided it's properly installed and maintained. Routine maintenance involves using non-acidic cleaners to remove dust and dirt, preventing mold growth. Damages can be repaired using specific adhesives, and if a section needs replacement, it can be cut out and replaced with a new piece. These adhesives also provide a vapor seal to prevent moisture penetration, potentially protecting the pipe from corrosion.
A farm faced a crisis when contractors accidentally damaged an underground heating pipe. Instead of a costly and time-consuming replacement, they used a universal pipe repair kit. The high temperature resistant tape was wrapped around the pipe, sealing the leak. A pipe repair bandage was then applied for added protection. The repair was completed in less than an hour, minimizing disruption and saving significant costs. This case highlights the effectiveness and efficiency of rubber pipe insulation in real-world scenarios.
Rubber pipe insulation, particularly flexible elastomeric closed-cell foam, offers a myriad of benefits, from lower thermal conductivity to higher continuous operating temperatures and predictable fire behavior. While the initial cost may be higher than other materials, the long-term savings in energy costs and maintenance make it a cost-effective choice for commercial and industrial applications. Proper installation and maintenance can ensure its longevity, contributing to the sustainability of heating systems by reducing carbon emissions. Real-world case studies further underscore its effectiveness and efficiency. In conclusion, rubber pipe insulation is a versatile, reliable, and sustainable solution for heat conservation and cost reduction.