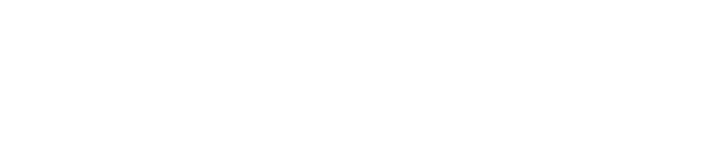
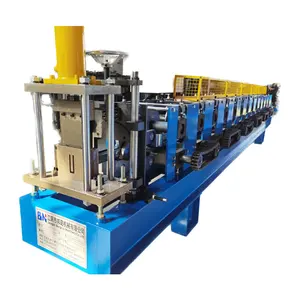
High Speed Light Steel Keel Drywall U Channel Stud And Track Roll Forming Machine C Channel Making Machine

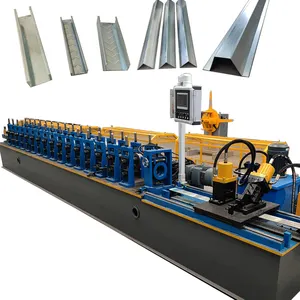
Drywall Metal Stud CD UD UW CW Making Machine Light Gauge Keel Stud Track C Channel Steel Roll Forming Machine


In the fast-paced world of construction, efficiency is not just an advantage; it's a necessity. Enter the realm of metal stud and track roll forming machines, the unsung heroes behind the skeletal frameworks of modern buildings. These sophisticated devices transform coils of metal into the studs and tracks that form the backbone of drywall systems, shaping the future of construction with every bend and cut. As we delve into the capabilities and applications of these machines, we uncover the technological advancements that are setting new standards in the construction industry. Join us in exploring how these innovative machines are revolutionizing efficiency and precision on the job site.
Metal stud and track roll forming machines are versatile equipment designed for the production of drywall channels, commonly referred to as studs, tracks, and omega channels. These components are integral to constructing economical wall and ceiling frames. The machines can be adjusted to work with varying material widths, allowing for the creation of studs or tracks as needed. Furthermore, they can be programmed to execute precise punching operations on both studs and tracks.
The machinery is engineered to operate with advanced control systems, ensuring consistent performance and quality in the final products. The adaptability of these machines is highlighted by their ability to produce different sizes of studs and tracks by simply feeding materials of various widths. For production lines with minimal size differences between studs and tracks, additional roller stations can be integrated, enabling the same machine to manufacture both components efficiently.
For larger-scale operations, it is recommended to utilize separate machines for studs and tracks to maximize production throughput. These roll forming machines are designed for ease of operation, featuring automatic functionality governed by PLC (Programmable Logic Controller) controls, which streamline the process from decoiling to forming, cutting, and finally running out the finished product.
The Alibaba platform showcases a diverse range of metal stud and track roll forming machines, catering to various construction needs. Among the types available, there are machines designed for creating high-precision metal studs and tracks, which are adept at handling wire sizes. For larger scale projects, robust solutions for producing metal framing components are offered.
Specialized options include machines tailored for light gauge steel framing, a crucial element in modular steel buildings. The versatility of roll forming equipment is demonstrated by its capability to produce complex fasteners and structural elements. Additionally, machines engineered for on-site construction provide flexibility and efficiency.
For ceiling applications, machines tailored to create precise framing components are available. The profiles for drywall metal stud and aluminium corner bead making machines, as well as the Light Gauge Drywall Making Machine, further expand the range, offering solutions for intricate detailing and lightweight construction. Lastly, machines designed for specific architectural applications are indicative of the specialized machinery available.
Metal rollforming is integral to various industries, playing a crucial role in modern construction. This process is essential for creating components like metal studs and tracks, which are fundamental in the structural framing of buildings. The versatility of rollforming allows for its application across multiple sectors, enabling the production of items ranging from metal roofing to complex automotive parts. The adaptability of rollforming machinery to produce long lengths of metal products in large quantities makes it indispensable for construction projects that demand precision and efficiency. As technology advances, the capabilities of rollforming continue to evolve, meeting the ever-growing needs of the construction industry.
Roll forming machines are integral to the production of uniform, high-volume products, with each component of the machine working in unison to deliver precise results consistently. These machines are particularly adept at handling coiled metal, shaping it into the desired cross-section profile through a series of tooling stations.
One of the standout features of roll forming machines is their inline capabilities, such as punching and stamping, which allow for a variety of operations to be performed during the roll forming process. This versatility is beneficial for producing metal studs and tracks, as it can accommodate high-strength metals without being constrained by the product's length, aside from the coil's size.
The design process for these machines requires a careful evaluation of the machine's capabilities against material costs and other expenses to ensure a profitable outcome. Material choice is critical, with aluminum and steel being popular for their durability and ability to maintain shape after manipulation. Other materials like copper, brass, and lead are also compatible with roll forming processes.
Considering tooling costs is crucial, as these are significant upfront investments. However, the long-term savings projected from the use of efficient roll forming machines often justify the initial expenditure. Additionally, the high efficiency and volume production capabilities of these machines underscore the importance of accurate forecasting to minimize errors and maximize business success.
Understanding the material and manufacturing requirements for light-gauge non-structural steel framing is crucial in the construction industry. These specifications are essential for ensuring the quality and performance of metal studs and tracks produced by roll forming machines. The specifications typically cover the dimensions, thickness, and strength of the materials used, which directly impact the durability and safety of the framing in various applications.
Additionally, the specifications for fire-rated partitions are an important consideration when selecting materials for metal studs and tracks. These requirements ensure that the materials will perform adequately in the event of a fire, providing an additional layer of safety in building design. By adhering to industry standard requirements, manufacturers can guarantee that their products are suitable for modern construction needs and comply with safety regulations.
Roll forming is recognized for its efficiency and precision in shaping metal, offering tight tolerances on complex profiles. This process, which involves a continuous bending operation, allows long metal strips to be passed through consecutive sets of rolls, incrementally shaping the metal to the desired cross-section. The inherent flexibility of roll forming means it can handle a variety of shapes and sizes, and it can be adapted to include secondary operations such as welding, punching, and precision laser cutting within the same production line.
The advantages of using advanced roll forming equipment include the ability to work with a wide range of material gauges and the capability to achieve precise bends, even up to 180 degrees, depending on the metal's ductility. This method is not only effective for creating complex shapes but also increases production efficiency by minimizing the need for additional handling and equipment. Furthermore, the integration of secondary processes streamlines production, potentially reducing operational and capital costs.
Navigating Alibaba.com for the best roll forming machines involves understanding the diverse range available. The platform offers a variety of roll forming machines, including those designed for creating metal studs and tracks, which are essential components in modern construction. From machines capable of producing door frames, C purlins, and steel coils to those specialized for roofing tiles and shutter doors, the selection caters to different industry needs. Prospective buyers can find equipment like the customizable roll forming machines, which can be tailored to specific requirements provided there are profile drawings. Alibaba.com's range includes machines for creating light steel frames, cable trays, and even high-speed C channel machines, reflecting the adaptability of roll forming technology. The site also lists machines capable of handling various materials and thicknesses, such as the 0.5-1.2mm galvanized steel machines for drywall applications. For those in the roofing industry, machines are available for producing glazed tiles, corrugated sheets, and ridge capping, demonstrating the versatility of roll forming equipment. When searching for the right machine, it's important to consider the specific applications and the type of metal parts required for your projects.
To maintain peak performance of metal stud and track roll forming machines, a consistent maintenance routine is crucial. This includes daily checks to ensure the coolant mixture is at the correct concentration, using a refractometer for accuracy. The mixture's balance is essential to prevent roller adhesion and maintain product quality.
Regular lubrication is also vital for smooth operation. Shear dies require daily lubrication, while roll former shaft bearings need monthly attention, and pillow and slide blocks should be serviced annually. This schedule is based on a machine running a two-shift operation over 250 days a year.
Hydraulic oils should be filtered through a 10 micron filter upon addition or change to remove impurities. The frequency of hydraulic oil replacement depends on usage, with typical changes occurring biannually. Operators should monitor oil levels regularly and change in-line hydraulic filters as indicated, preferably when the indicator is in the yellow range, to avoid compromised filtration.
Cleaning the reservoir is also a part of the maintenance process, helping to eliminate impurities that could affect the machine's performance or the quality of the finished product. Adhering to these maintenance tips will help ensure the longevity and efficiency of your roll forming machine.
In conclusion, metal stud and track roll forming machines represent a significant leap forward in construction technology. Their ability to produce high-quality, precise components quickly and consistently makes them indispensable in modern construction. From the adaptability to handle various material gauges to the integration of advanced control systems, these machines offer a plethora of features that enhance production throughput. The Alibaba.com platform serves as a crucial resource for sourcing these machines, providing a wide selection to meet diverse construction needs. Proper installation and diligent maintenance are key to maximizing the potential of roll forming equipment, ensuring long-term performance and reliability. As the construction industry continues to evolve, the role of metal stud and track roll forming machines will undoubtedly expand, driving efficiency and innovation in building practices worldwide.